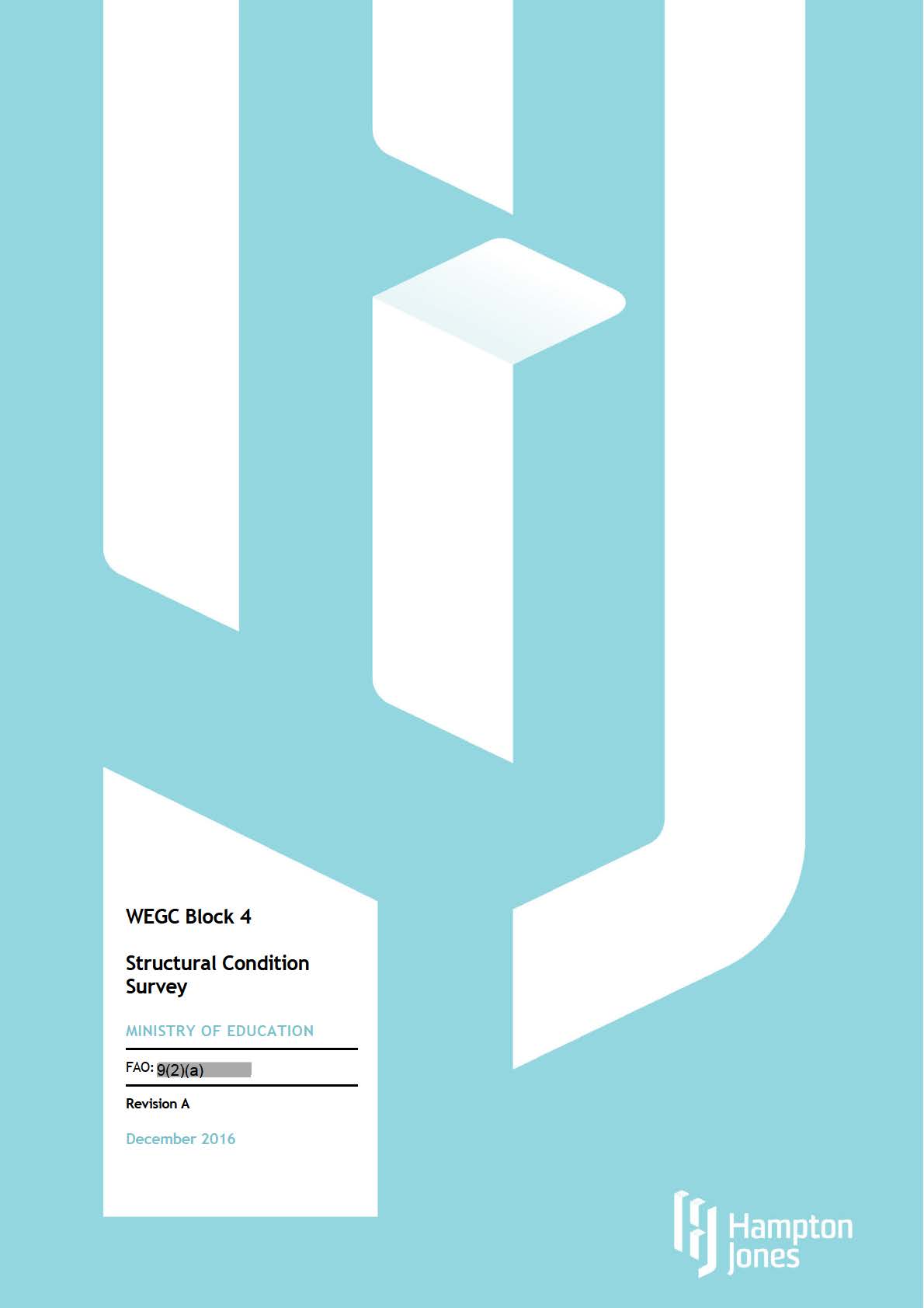
under the Official Information Act 1982
Released
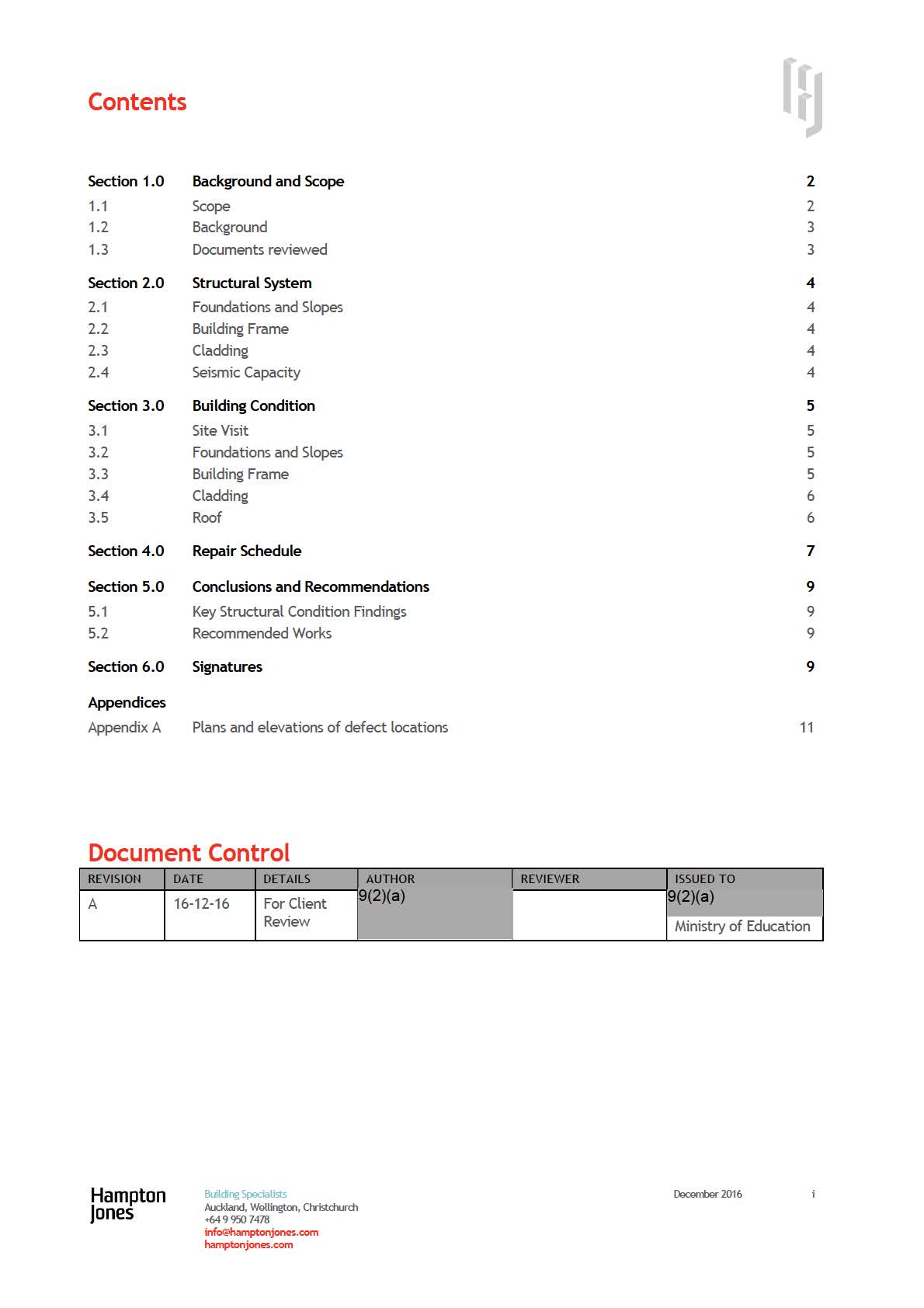
under the Official Information Act 1982
Released
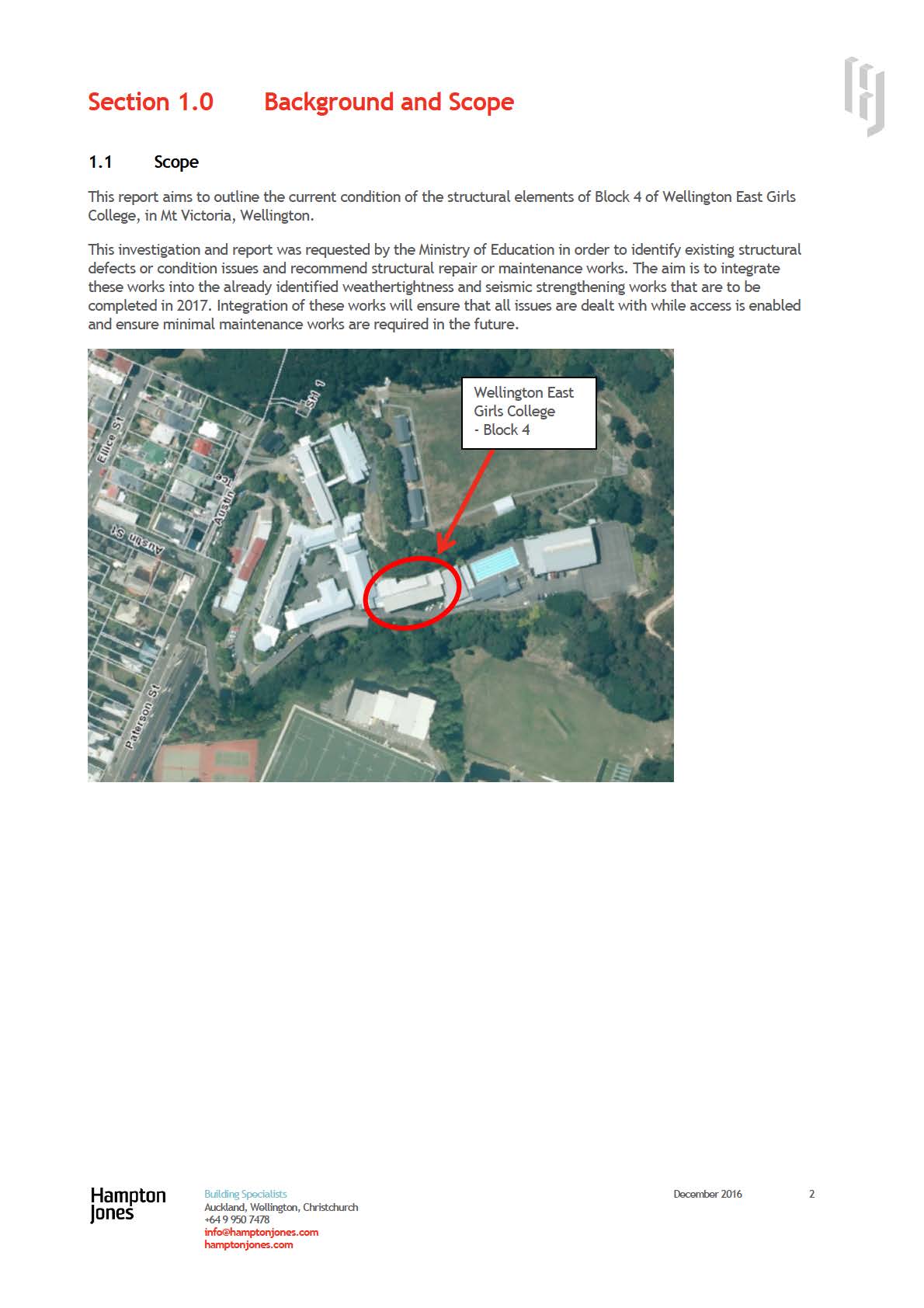
under the Official Information Act 1982
Released
1.2
Background
Reports have been produced on this building detailing the building fabric condition, weathertightness defects
and issues and the seismic capacity of the building. It was one of these reports that noted there were signs of
deterioration to the structural members.
Wellington East Girls College was established in 1925. There are a number of different blocks and buildings built
at varying times. Block 4 was originally built in 1964 and was extended in 1999. The 1999 extension included
some strengthening work as well as internal alterations and timber framed extensions.
1.3
Documents reviewed
The documents reviewed were sourced from the Wellington City Council archives property file and also as
provided by Opus who have completed a DSA on this building. A good level of structural and architectural
documentation is available for both the original buildings and the later alterations. It is assumed for the
purposes of this report that these drawings accurately represent this building as it stands today.
The Detailed Seismic Assessment completed by Opus in Jan 2016 was also reviewed as part of this report, but
only for the purpose of identifying critical elements and areas where proposed repair works may be affected by
seismic strengthening works. The Opus Geotechnical report for the site was also reviewed for information only.
under the Official Information Act 1982
Released
Building Specialists
December 2016
3
Auckland, Wellington, Christchurch
+64 9 950 7478
[email address]
hamptonjones.com
Section 2.0
Structural System
2.1
Foundations and Slopes
The building is generally supported on shallow pad footings and ground beams except at the northern
side if the building. The building platform is a bench cut into the original slope, at the northern side
of the building there is a small area of fill, piles were installed at this location to provide founding on
competent material rather than fill.
2.2
Building Frame
The building structural system is a mix of concrete and block walls and a concrete frame.
The ground floor slab is a suspended slab that spans between ground beams.
The first floor slab is made up of an in-situ concrete slab that spans between the concrete frames.
The roof is a lightweight steel cladding supported on timber purlins which span between concrete
frames.
2.3
Cladding
The external cladding of the walls is generally glazing and lightweight panels. The original precast
cladding panels remain at the ground floor at the rear of the building and as partial height spandrel
panels at the front of the building.
The precast spandrel panels to the front of the building do not contribute to the seismic or gravity
load resisting capacity of the building. The precast panels are attached to the concrete frames with
steel dowels and there is a movement gap between the concrete frame and panel.
2.4
Seismic Capacity
Seismic and lateral capacity is provided by the concrete frames and concrete/block infill walls. Cross
bracing at roof level distributes lateral forces to the frames. The concrete slab at first floor level acts
as a diaphragm as does the ground floor concrete slab. The concrete frames act as portal frames in
the transverse directions and in the perpendicular direction infill walls transfer lateral forces to the
ground.
under the Official Information Act 1982
Released
Pictures 1 and 2 – External view of the front and rear of Block 4
Building Specialists
December 2016
4
Auckland, Wellington, Christchurch
+64 9 950 7478
[email address]
hamptonjones.com
Section 3.0
Building Condition
3.1
Site Visit
A site visit to assess the condition of the building was conducted by Jennifer Critchley on 30-11-16
All rooms in the building were accessed but inspection was limited to visible elements only. No
finishes were removed during this investigation and limited inspection at height was undertaken.
There were some indicators of hidden structural deterioration (rust staining etc.) and it is expected
that some defects will be discovered during opening up for the weathertightness and seismic
strengthening works. It is recommended works that some contingency be allowed within budgets both
for physical works and engineering support to identify and investigate these defects and specify
appropriate repairs/treatment as required. Assessment of Structural Condition
3.2
Foundations and Slopes
The slope to the rear of the building has been cut back to a safer angle at the rear of the building.
There are signs of fretting from this slope but steel fences are assumed to catch any larger sections
that come loose. Also, the area to the rear of the building is not generally accessible to students and
is used for maintenance access only as a rule.
The slopes to the front of the building are steep but there are no signs of instability and the top of
the slope is a reasonable distance away from the front face of the building.
Geological maps produced by Opus suggest that the boundary of fill placed in front of the cut into the
bank to create the building platform is unlikely to extend far if at all under Block 4.
In general, there are no visible signs of settlement of the building. There are no visible cracks or
deformations of the ground adjacent to the building. The columns and floors appear straight and
level. Little of the ground floor slab was visible but it is likely that any significant deformations would
be detectable through the linoleum flooring.
3.3
Building Frame
The building frame appears to be in generally in good condition except for a couple of isolated areas
and the junctions between the original and later concrete structure.
A-Build sheet S4 notes a new soffit has been cast against the original concrete at grids 1, 5 and 11.
However, from review on-site it appears that this detail was installed at Grids 1, 4, 5 and 11. At each
of these locations, there are signs of moisture ingress at the concrete cold-joint and cracking of the
concrete and rust staining are evident. Moisture ingress is evident at all of these locations and it
appears that moisture has been tracking into the building along this joint detail. It appears that these
under the Official Information Act 1982
areas have been cleaned and painted a number of times so the extent of the underlying damage is
difficult to determine. However, as long as no concrete has spalled and there are no cracks greater
than 5mm, the repair methodology will not change.
Additionally, even where no new soffit has been installed, the joint between the new column and the
underside of the original beam/column is showing similar signs of moisture ingress at all locations
where this detail occurs. Less severe corrosion and staining than at the soffits is evident but it is
possible defects have been hidden under new coatings. Sealing of this joint is required.
Released
Building Specialists
December 2016
5
Auckland, Wellington, Christchurch
+64 9 950 7478
[email address]
hamptonjones.com
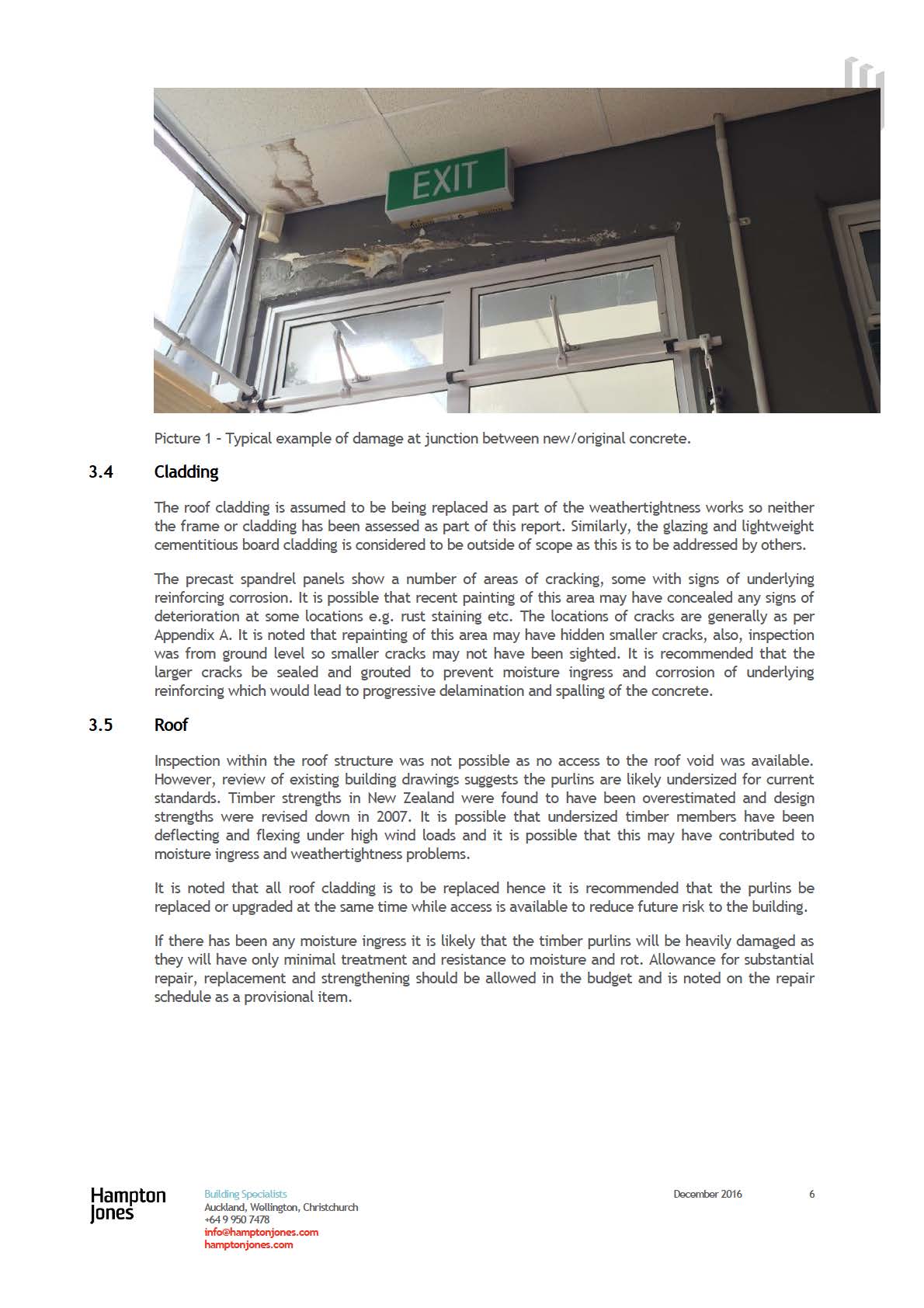
under the Official Information Act 1982
Released
Section 4.0
Repair Schedule
Refer to Appendix A for plans and elevations showing locations of defects.
DEFECT
DESCRIPTION
REPAIR/REMEDIATION
NO.
1 to 4
Deterioration of the new to original concrete
Concrete in this area should be cleaned of all
joint at the underside of the original cantilever
finishes to both internal and external faces.
beam. Moisture ingress through this “cold-joint”
Assess condition of concrete once exposed.
has tracked moisture inside the building, damage Assuming no major spalling and cracks less than
finishes and caused deterioration of the
5mm, pressure grout and seal the joint from both
reinforcing across the joint and has caused
sides.
efflorescence and minor spalling at the face of
Refer to Appendix B for detailed specification for
the joint.
repair.
5
Deterioration of the new to original concrete
As per Defects 1 to 4.
joint at the interface of the top of the new
concrete column and the underside of the
original cantilever beam. Moisture ingress
through this “cold-joint” has caused
efflorescence. There is potential for there to be
rust staining and deterioration of the reinforcing
across this joint but re-painting of the surface
will have obscured this.
6
Small vertical crack and small isolated spall in
As per Defects 1 to 4.
precast spandrel cladding panel.
Spall is likely to be due to moisture ingress
through the crack into an area where there is a
section of shallow reinforcing.
Movement joints at ends of precast panel are to
be reviewed as part of the detailed design of
seismic strengthening. Original detailing of a stiff
mortar joint at the ends of these panels may
have contributed to the cracking noted in the
precast panels on this elevation.
7
Small horizontal crack and rust staining.
Defect to be more closely inspected during
Similar to defect 6 except there are signs of
construction.
deeper seated cracking given the level of rust
May require a more intrusive repair or removal of
staining.
the window panel to allow sealing of a hidden
crack as per Defects 1 to 4.
8
Minor vertical crack.
As per Defects 1 to 4.
Similar to defect 6 except no spalling present in
this area.
9
Large spall and exposed reinforcing to lower edge Clean area of finishes, remove any additional
under the Official Information Act 1982
of a concrete spandrel panel.
loose concrete and scabble surface.
Similar to defect 6 but has deteriorated.
Wire brush clean and coat any exposed
reinforcing with Sika MonoTop 910N.
Patch concrete with Sika MonoTop Rapid.
10
Minor horizontal crack.
As per Defects 1 to 4.
Similar to defect 6 except no spalling present in
this area.
11
Bulging of paint finishes in the concrete lintel
Remove finishes from concrete in this area to
above the window to the stairwell.
establish if any cracking or reinforcing corrosion is
Released
It is noted that there are water ponding issues to
present.
Building Specialists
December 2016
7
Auckland, Wellington, Christchurch
+64 9 950 7478
[email address]
hamptonjones.com
the adjacent roof and timber parapet above has
Assuming no corrosion is present, coat surface of
deteriorated and is expected to be fully replaced. concrete with Sikagard 740 S and allow to cure
No evidence of rust staining but removal of
before applying architectural finishes.
finishes is required to confirm this.
Suggest apply a sealant coating to reduce
likelihood of reoccurrence of efflorescence.
12
Rust staining and cracking to a small patch of
As per defect 9.
concrete beneath a downpipe.
Likely due to a localised area of shallow
reinforcing and exacerbated by dripping water
from the downpipe.
13
Rust staining to an extended length of concrete
Remove finishes to concrete to assess if any
beam. Not clear where this staining originates,
cracking or spalling of concrete beneath coatings.
does not appear to be any concrete deterioration Investigate potential sources of rust staining once
(cracking, spalling etc.).
local cladding finishes are removed.
Suggest re-assess when adjacent finishes are
Any repair (if required) is likely to be as per
removed, corrosion of fixings behind claddings
defects 1 to 4.
could be the cause of the staining.
14
Small but deep spall to concrete with exposed
As per defect 9.
and corroding reinforcing.
Likely due to a localised area of shallow
reinforcing.
Roof
Likely to be presence of rot in some or all of
Allow a provisional sum for replacement of 50% of
purlins timber purlins. Timber purlins are also undersized timber purlins and infill between with additional
and may be contributing to movement of
purlins.
claddings and weathertightness issues.
OR
Replace all timber purlins with stronger sections
under the Official Information Act 1982
Released
Building Specialists
December 2016
8
Auckland, Wellington, Christchurch
+64 9 950 7478
[email address]
hamptonjones.com
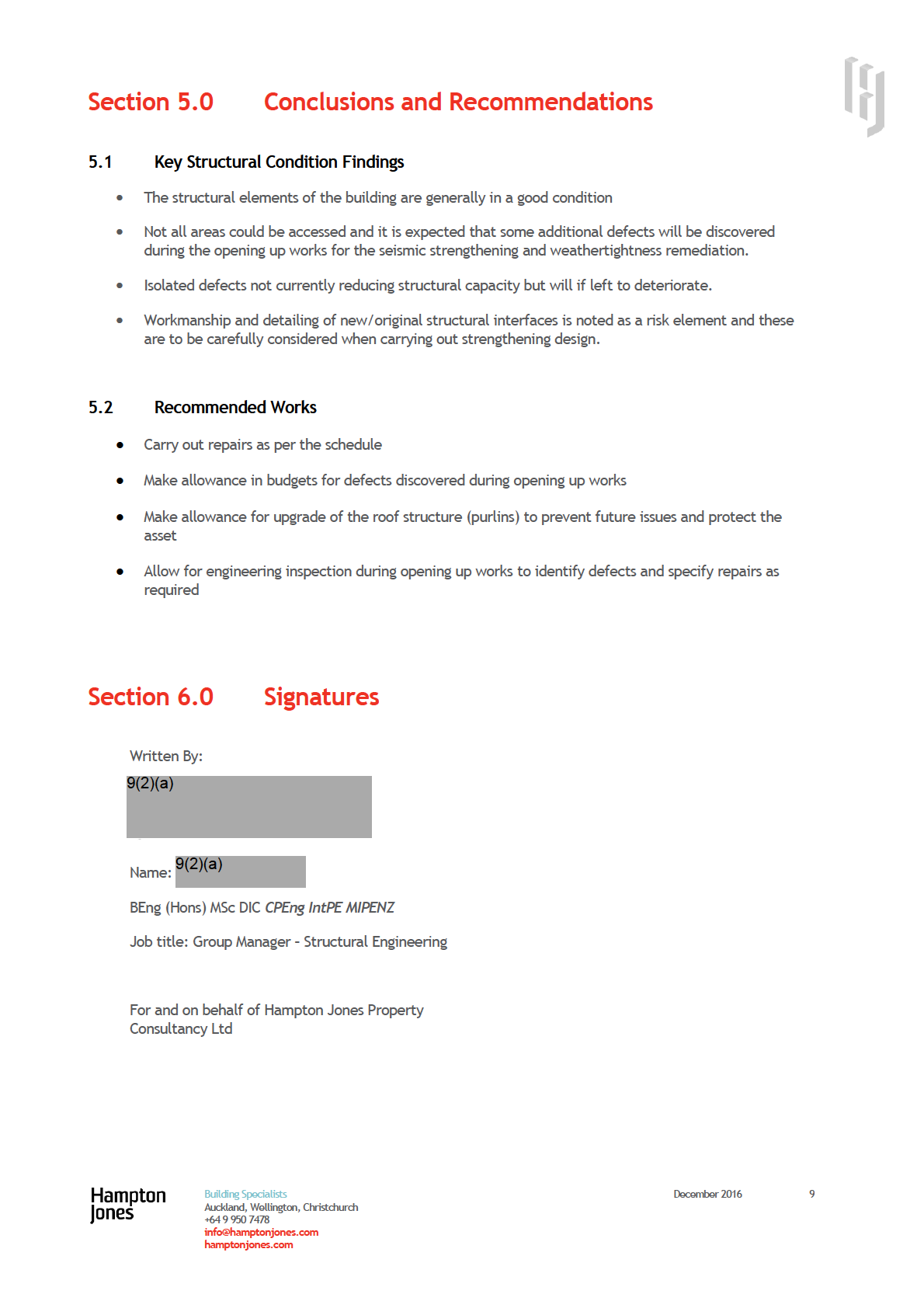
under the Official Information Act 1982
Released
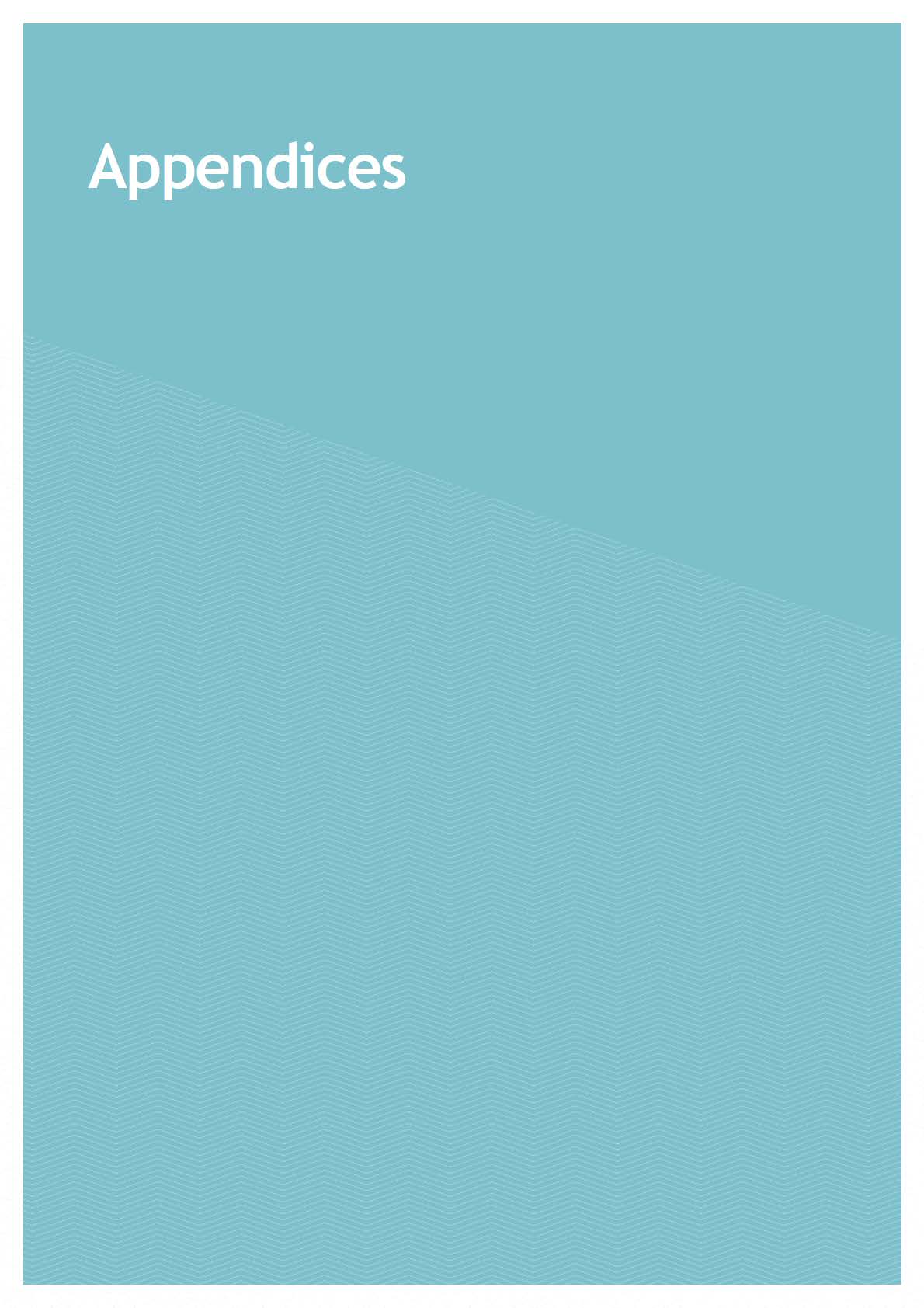
under the Official Information Act 1982
Released
Appendix A
Plans and elevations of defect locations
under the Official Information Act 1982
Released
Building Specialists
December 2016
Appendices
Auckland, Wellington, Christchurch
+64 9 950 7478
[email address]
hamptonjones.com
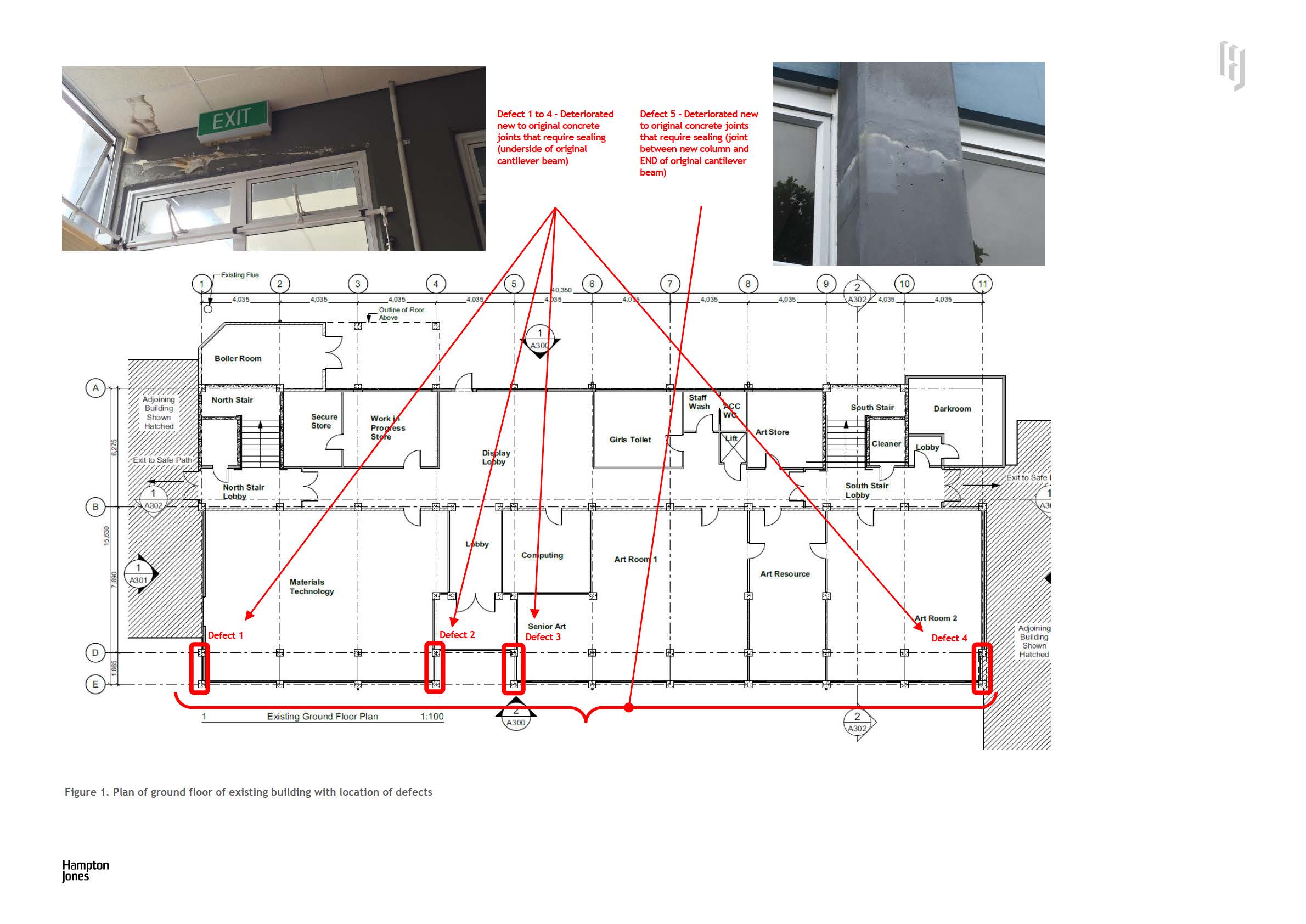
under the Official Information Act 1982
Released
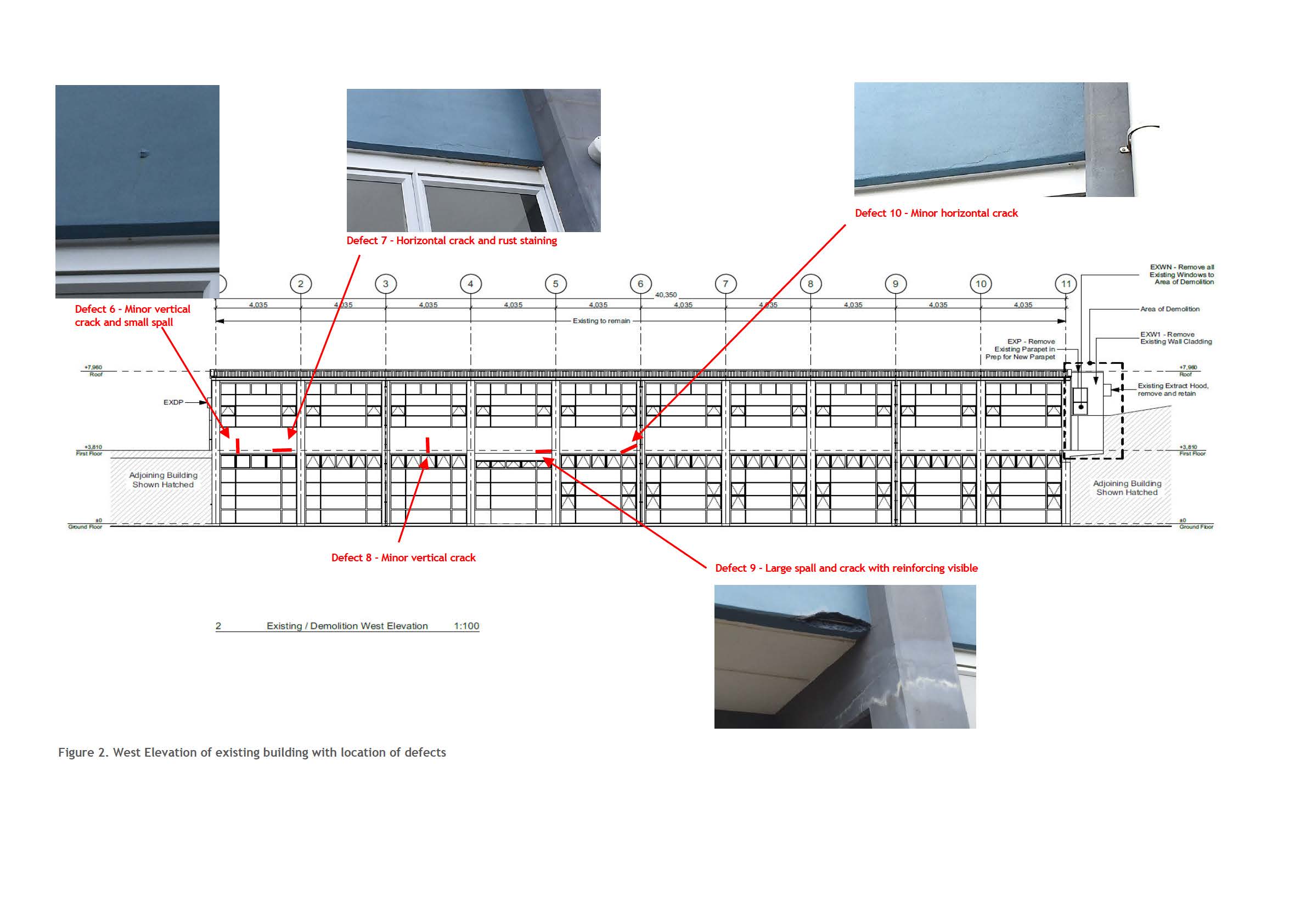
under the Official Information Act 1982
Released
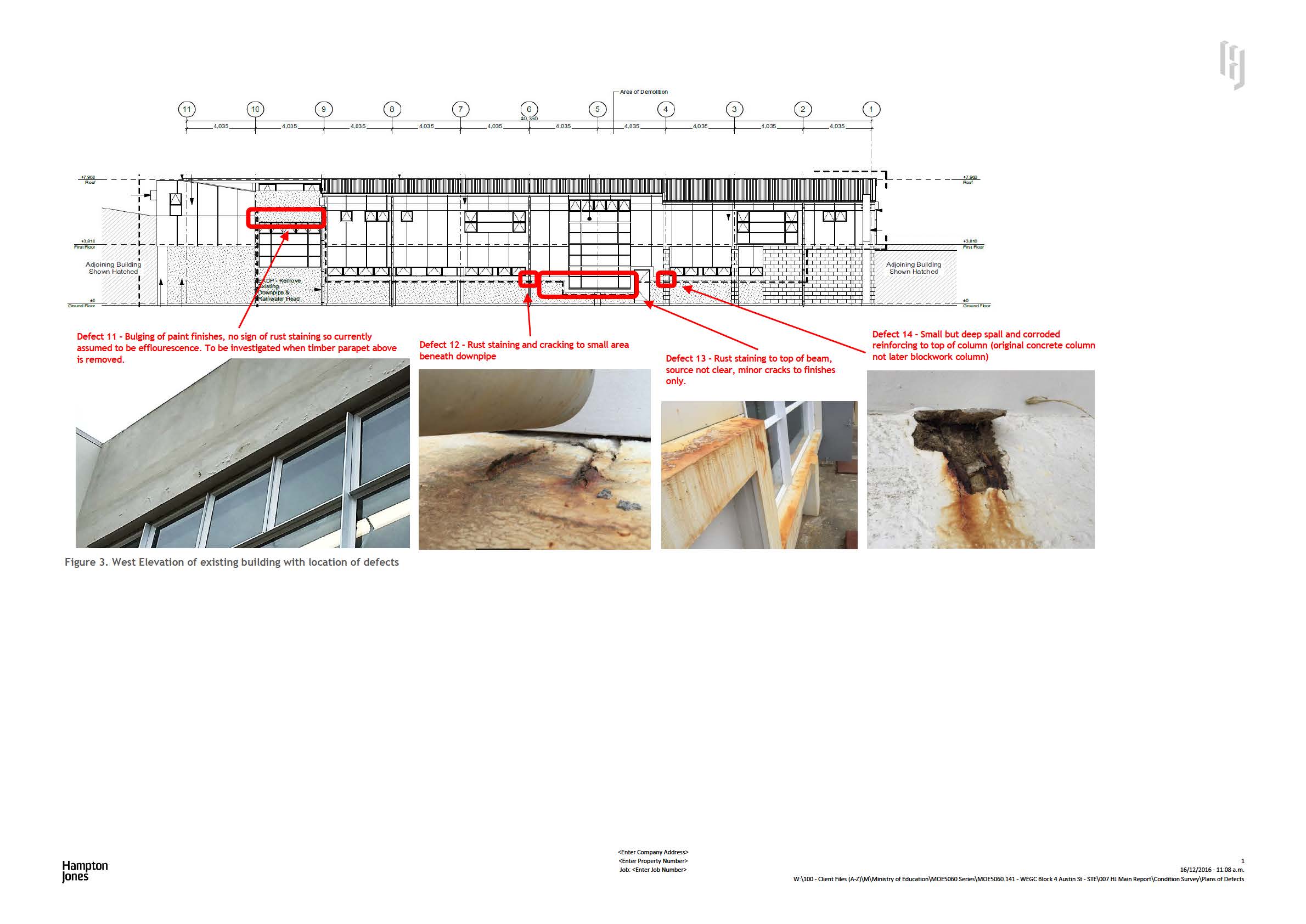
under the Official Information Act 1982
Released
Appendix B
Specification for pressure grouting of
cracks/joints
All cracks identified in concrete elements are to be carefully recorded as per the requirements of section 4.1.
Cracks to concrete: 0-0.2mm
Isolated hairline cracks of 0 to 0.2mm are considered superficial and no risk to structural integrity and are note
required to be noted on the Contractors Inspection. However, if a large number of closely spaced cracks are
found, please inform the engineer.
If cracks are external, sealing of cracks for durability only is required. Use an epoxy adhesive sealant such as
Sikadur 31CF and follow all manufacturer’s instructions on preparation and application etc.
If cracks are internal, no repair is required other than to repair and reinstate the surface finishes as per the
architectural requirements.
Cracks to concrete: 0.2-2mm
Isolated small cracks are not general considered to be a risk to structural integrity. If the scale and number of
cracks found is beyond that anticipated in the schedule of works, the engineer must be informed before work
commences.
All cracks 0.2-2mm will require repair by injection of an epoxy resin.
Where access is restricted and sealing around the crack is not possible, use a thixotropic epoxy resin such as
Sikadur Injectokit – TH
Where access is possible to both sides of the crack, use a low viscosity epoxy resin such as Sikadur Injectokit –
LV or Sikadur 52.
Cracks to concrete: 2-5mm
Large cracks 2-5mm will likely require repair by injection of an epoxy resin identical to specification for cracks
0.2-2mm. However, it is currently assumed that none of the cracks observed on-site appear to be greater than
2mm wide (except cracking to plaster render to Green Room Foundations which is non-structural) and
additional structural capacity and integrity checks and additional works may be required.
All cracks 2-5mm are to be noted on the Contractors Inspection and highlighted to the engineer BEFORE repair
works commence.
Cracks to concrete: 5+mm
Very large cracks greater than 5mm will likely require special consideration. These must be noted on the
Contractors Inspection and highlighted to the engineer BEFORE repair works commence.
Assuming no overriding structural integrity issue requires more invasive repairs, it is likely that repair
specification will take the form of injection with Sikadur 42 or Sika Grout 212.
under the Official Information Act 1982
Released
Building Specialists
December 2016
Appendices
Auckland, Wellington, Christchurch
+64 9 950 7478
[email address]
hamptonjones.com